Así se arma la carrocería de un auto de TC
El especialista Pablo Morales le contó a SoloTC secretos del armado de las carrocerías de los autos de TC. Qué materiales usan, en cuánto tiempo los arman y todos los detalles en esta nota.

El enchapado de un auto de Turismo Carretera requiere de un verdadero trabajo artesanal, para darle la forma original a cada modelo de auto. Para conocer cómo es el proceso, SoloTC habló con el especialista Pablo Morales, quien desde su taller en Arrecifes es el encargado de armar la mayoría de las carrocerías de los autos de la “máxima” y el resto las divisionales de la ACTC (TC Pick Up, TC Mouras y TCP Mouras). ¿Qué materiales utilizan? ¿Cuánto tiempo tardan? ¿Los autos mantienen alguna parte original? Te contamos todos los detalles en esta nota.

Para realizar el enchapado se emplean plantillas con la misma matriz que utiliza la Técnica de la ACTC para controlar diferentes parámetros de la carrocería. En el proceso de construcción se utiliza chapa lisa Nº24 de 0,5 milímetros de espesor.
“Cuanto más liviana sea, mejor será la presentación del trabajo”, explicó Morales. El 80% de la carrocería se realiza con planchas de esta medida. “En algunas partes como el torpedo y la bajada del parabrisas se usa una Nº22 que tiene un poco más de espesor”, agregó.
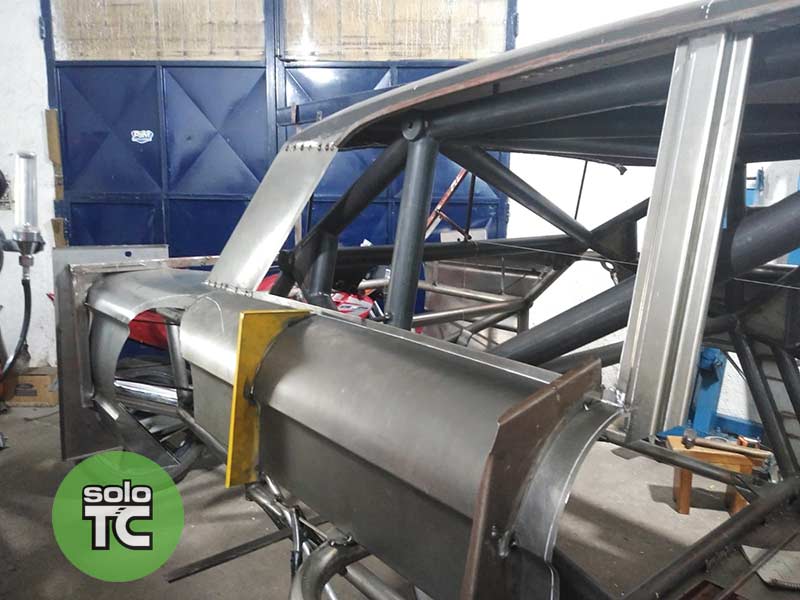
Una vez recibida la estructura se coloca en un banco de trabajo, también llamado cuna. El primer paso es posicionar la medida correcta del techo. “Una vez posicionado se establece la medida con respecto al anclaje, lo que llamamos el punto 0, que es la clave para que el auto quede en total simetría”, contó. Luego se determina una escala de altura delantera y trasera. “En nuestro caso, una vez determinado el grado de la luneta, se coloca el torpedo trasero que divide la luneta del baúl”, explicó.

El enchapado se realiza en forma artesanal con un ‘martillo aguantador’ y caños. “Para algunas partes del auto suelo usar un palo de escoba. La clave no es pegar por pegar, sino hacerlo en el lugar justo y darle el ‘cariño’ que se necesita para adaptarlo a lo que se busca”, explicó Morales que por lo general realiza todo el trabajo con 1 solo ayudante, Ricky, un empleado de 19 años. “En épocas de intensa actividad convoco a 2 colaboradores más: Oscar Crocco y el Pela Velázquez. Y durante muchos años trabajó conmigo mi hijo Gamaliel, que durante los fines de semana también me ayuda”, agregó.

“Hay autos que tienen terminaciones más complicadas. Lo más complejo es la bajada de la Chevy porque siempre me gustó que mantenga el dibujo original. Hay que trabajarlo con un martillo, en la jerga se llama ‘tranchar la chapa’, se le da la moldura. Con la cabecera también se pierde mucho tiempo porque es la terminación que le das al trabajo”, aclaró Morales.

Las planchas se cortan en el mismo taller. Depende del tiempo del que dispongan se va armando un stock de diferentes partes del auto. “A veces estamos más holgados y plegamos un guardabarros o panel de puertas. En caso de estar más apretados con los tiempos, se van preparando las piezas a medida que armamos el auto”, explicó Morales.
Entre las 4 marcas tradicionales lo único que es original es el techo. “Hay que rastrearlos por todo el país, los más complejo de conseguir son los de Chevrolet o Dodge”. El resto se fabrica todo a partir de las planchas de chapa y las matrices. “Distinta es la situación del Toyota Camry, en este caso es necesario usar las pieles originales porque tiene muchas líneas. Estamos hablando de un auto con una tecnología mucho más avanzada”, explicó el especialista.

Desde que reciben la estructura tubular hasta que el auto se entrega con toda la carrocería armada pueden pasar entre 17 y 21 días, depende de la carga de trabajo que haya en el taller. Según le contó Morales a SoloTC, desde que se comenzaron a construir las estructuras de nueva generación en 2015, armó alrededor de 50 vehículos entre las diferentes categorías de la ACTC.
En 2011 la ACTC digitalizó las medidas de los autos originales que compiten en el TC. Con el brazo Faro se hizo un relevamiento dimensional de las carrocerías de un Ford Falcon, un Torino 380W, un Chevrolet Chevy y un Dodge GTX de calle, con el objetivo de tener documentación para evitar la deformación de los modelos en el proceso de fabricación.